355 < d 1600
– Below instructions should be followed absolutely step by step.
– We recommend using pipes with limited dimension tolerance range.
– The fusible pipe series are shown in the SDR labeling on coupler.
– Installation technician must be trained and certified to install Tega large diameter couplers.
– Fusion with other pipe materials such as PP, PVC etc. is not possible.
– Installation can be done at ambient temperatures between 0 °C and +45 °C. If ambient temperature is not within these limits use of welding tent is required.
– For general safety reasons, keep a distance of min. 1 m to the fusion site during fusion process.
– Make sure equipment that requires calibration is calibrated
– Fitting should be inspected for damage before installing
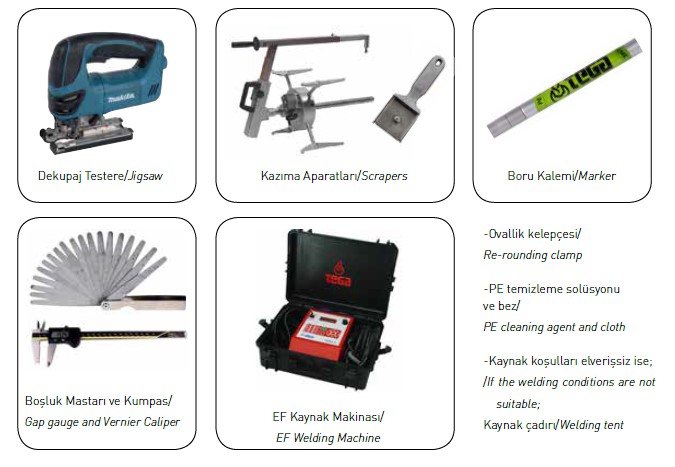
For the pipe cutting, a suitable cutter for plastics must be used. The pipes are to be cut square with this cutting tool.
ıf the pipe is not cut at right angles, fusion coil partially may not being covered by pipe, which causes uncontrolled flow of molten due to overheating. (Fig. 1)
2. Marking the fusion zone:
Fusion zone which is the insertion depth of coupler, must be marked with a marker on the pipe end or on the spigot end. Measure the total length of coupler and calculate the
half length. (Fig. 2) Mark the coupler half length + 10 mm on pipe surface (Fig. 3)
3. Controlling ovality
PE pipes may loose their roundness during storage. For this purpose measure pipe ovality as illustrated in Fig. 4 and 5.
If pipe is out of round or has a flat spot, use of the rerounding clamp is required (Fig.6).
After installation of the re-round clamp, check roundness of pipe against measuring pipe diameter. If pipe is still oval, re-position the rerouding clamp (Fig. 7 and 8).
4. Scraping The Pipe Surface
In order to remove the oxide layer of the pipe, scrape carefully the fusion zone (Fig. 9).
In order to remove the oxide layer completely, the pipe must be scraped so that shavings are formed and marking line
is removed.
The prepared surface must be protected against unfavorable weather conditions.
After that,the internal edge must be deburred and the outer edge rounded off as illustrated in fig.10
5. Degreasing of the Fusion Zone:
Remove coupler from its packaging without touching the fusion surface. Make a visual check to ensure coupler is undamaged (Fig.11).
The prepared pipe end or spigot end and internal face of coupler must be degreased with a suitable cleaning agent and a white absorbent and nonfibrous cloth (Fig. 12 and 13).
As a cleaning agent; isopropyl alcohol can be used (The alcohol content mustn’t be less than 96% by volume).
Degreased surfaces must be protected against dirt or unfavorable weather conditions.
6. Inserting of the pipe end or spigot end into the coupler:
Push coupler onto pipe up to the marking zone (contact terminals of coupler must be easily accessible).
Do not let pipes support their own weight in the coupler (if necessary support under pipe).
Prepare the second pipe same as first one and follow same steps.
Ensure coupler and pipes are both on the same axis (Fig.14). Ensure tension-free fixing of the joint. A non-tension free joint may result in a defective joint during fusion.
Check the gap between pipe and coupler on whole circumference. Use metal sticks to distribute local gaps (length of sticks must be 30 mm max)( Fig. 15). So ensure equalized gaps on whole circumference. Measure gaps all around the pipe. If it is less than 2 mm pass Fusion procedure.
7. Fusion:
Provided that information given in instructions are followed step by step, connect fusion cables to the terminals of the first side of the coupler (Fig.16). Fusion parameters are contained in the main barcode. Fusion data can be transffered to machine by using reader (Fig.17).
After reading of barcode, compare data on barcode and data shown on display. Start fusion process. Wait until cooling time has elapsed before moving pipe and coupler. Cooling time is given on barcode and identified by CT.
As a safety precaution, be careful to stay at least 1 m away from the fusion area.
If the fusion process is interrupted for any reason (e.g. due to power failure) the fusion process can be repeated after the joint cooled adequately. Find these cooling times on TEGA Couplers’ barcode labels.